Guest Blog: Technology developments in the damage management restoration industry
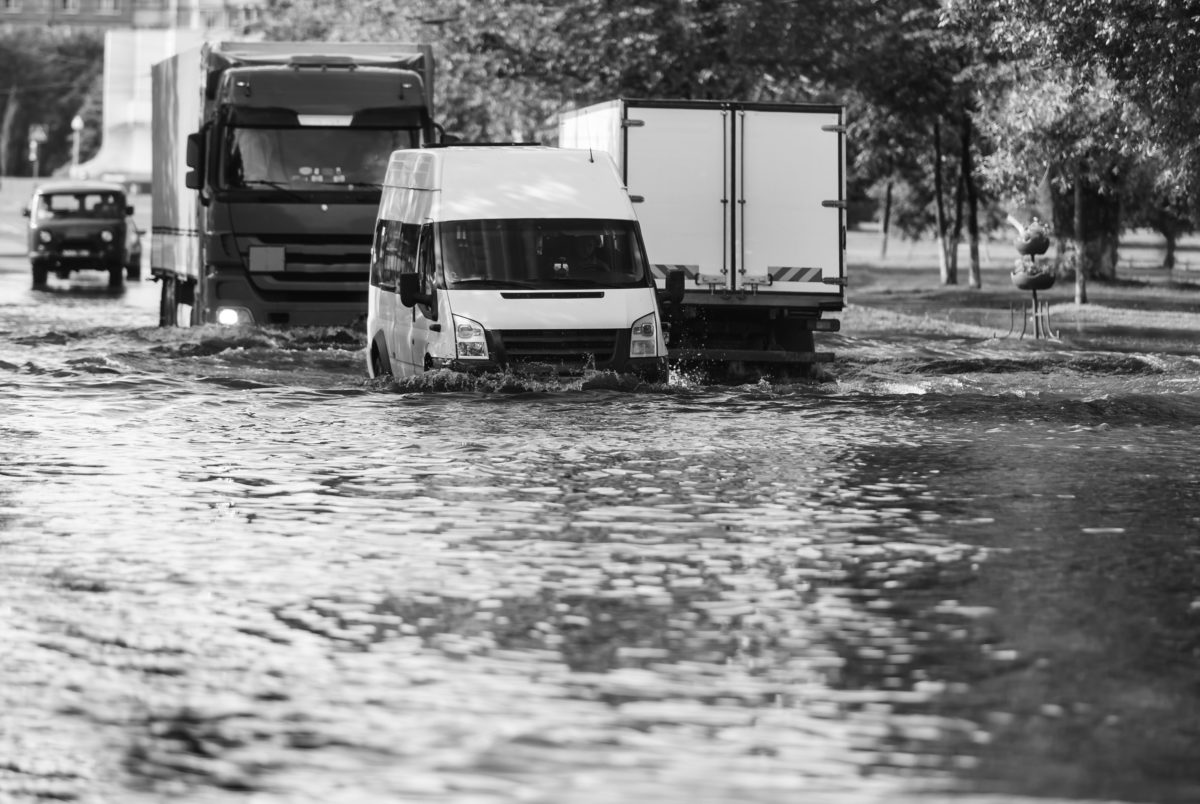
By Neale Vickery, Corroventa.
Over the last decade big investments in time, money and intellect have been made by damage management equipment suppliers to offer improved performance and to improve energy efficiency.
The latest designs and technologies have helped to improve dehumidification performance, so enabling drying projects to be completed in shorter time frames or with less equipment – or ideally both.
Equipment now available is more energy efficient and has built-in smarter technology which evaluates the incoming moist air intake and will automatically adjust its performance to minimise power consumption whilst maintaining maximum drying potential. Equipment is now being designed and manufactured to be lighter, smaller and more ergonomic, so it can be stored and transported easier and to enable technicians to transfer and position the equipment, with the intention of minimising the disturbance to the home owners.
As noise and homeowner disturbance is one of the major reasons why homeowners/ policyholders are moved into alternative accommodation by insurance companies (particularly when phrases like constant noise is mentioned), equipment manufacturers have invested enormously in noise reduction technologies to reduce and/or minimise any disturbances caused. At Corroventa, we have developed and manufactured equipment quiet running modes which can be programmed using the timer functions to run at required time slots to minimise homeowner disturbance. For example,
running quiet mode in the lounge during mid to late evening when the room is generally in use, and then running it at full operational power outside these required hours. This is technology that is already available across our industry, but what about the future?
Over recent months I have had great pleasure in meeting people from across our industry, ranging from directors and business managers from insurance companies, claim handling companies, directors and owners of damage restoration companies, to surveyors, loss adjusters, business managers and damage restoration technicians. The one question I get asked more than any other
is, “What do I see the greatest development being that will affect our industry over the next five to ten years?”. Most people asking this question believe that it will be difficult for me to answer but the truth is the opposite. The answer is very simple – Remote Monitoring. Remote monitoring and data logging systems are available widely from several different equipment suppliers and manufacturers.
We are now all using our smart access television systems and controlling our central heating systems whilst away from the home and even watching people coming to our homes using smart doorbell systems or surveillance systems via our smart phones or tablets. Surely as an industry over the next five years we can move towards 24-hour
information and moisture monitoring of our claims, rather than still basing our regimes on a short-term visit to the property by a technician every seven days.
Remote monitoring can provide you with a complete overview, identifying daily moisture fluctuations, providing accurate comparisons of the same moisture point and can even identify if equipment has been turned off or is being turned on and off by the homeowner as it conflicts with their lifestyle. Remote monitoring is beneficial to all parties in a claim, avoiding unnecessary visits to site by the damage restoration companies who instead will be able to plan site visits when required rather than to comply with an SLA.
Homeowners’ experiences will be improved as they no longer need to wait in for a technician to visit unnecessarily and can be updated directly on a regular basis from the damage restoration companies or even be provided with the visibility of drying reports.
Remote monitoring will also provide complete visibility of the claim to the insurer or alternatively detailed updates can be provided at required points or as and when required at the touch of a button. Information is recorded and retained for future use if required, which provides a completely transparent drying record. Corroventa’s remote monitoring system is called Supervision, and all recorded data is stored on the Amazon Cloud server for secure and permanent record. It also enables us to remote control our ES Range equipment.